盖世汽车讯 据外媒报道,跨国汽车制造商宝马集团(BMW)宣布,其增材制造工业化和数字化(IDAM)项目取得成功。
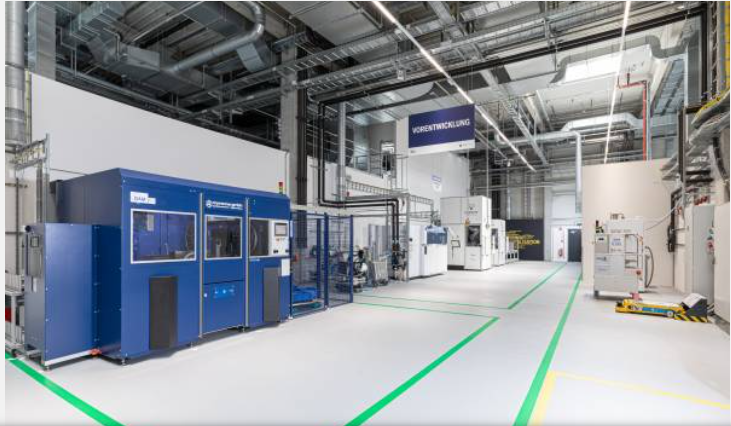
(图片来源:宝马集团)
三年前,由德国联邦教育与研究部(BMBF)资助、宝马集团牵头的项目联盟成立,其中包括一众中小企业、大型公司和研究机构。该联盟的共同目标是彻底改变汽车标准生产过程中使用的金属3D打印技术。
该联盟的12位成员展示,在宝马集团位于德国慕尼黑上施莱斯海姆(Oberschleißheim)的增材制造园区成功实施IDAM项目。该园区建立了一条数字连接的全自动3D打印生产线,为汽车标准化生产做准备。另外一条生产线位于波恩(Bonn)的吉凯恩粉末冶金公司(GKN Powder Metallurgy)。
通过激光粉末床融合(LPBF)3D打印,每年可经济有效地生产5万个普通部件,还可制造1万多个单独的新部件。在各级需要创建固体组件的地方,用激光将初始材料(金属粉末)逐层重熔。这种3D打印工艺大大增加了生产灵活性,因为不需要使用某些工具,即可实现新的设计可能性。
从2019年的概念大纲开始,目前全自动无人驾驶运输系统(FTS)可在IDAM生产线的模块之间运载3D打印机的移动构建室。这些机器由中央控制单元协调,整合来自各生产线模块的所有生产数据,以确保充分提高生产率和质量。
在该项目的实施过程中,研究人员开发了自动化生成3D打印构建数据的创新概念。现在,全自动模块可将加工后的金属粉末输送到工作区,独立准备材料。在专门设计的工作区,对制造部件进行后续处理,这些区域也是完全自动化的。一切以保证零部件质量为准则。
在激光熔融过程中,通过传感器在线检测成品部件的质量,其中包括用CMOS摄像头和高温计检查熔池排放。人工智能算法可将所收集的数据与实际部件质量相关联,在生产和部件质量评估过程中识别过程偏差。
受益于所有项目合作伙伴的专业知识,该项目才得以成功实施。在机械和工厂工程、部件设计和金属3D打印领域,这是实现数字化和自动化的唯一途径。
本文来源:盖世汽车资讯